Custom Components For The Medical
Rapid Manufacturing on Demand
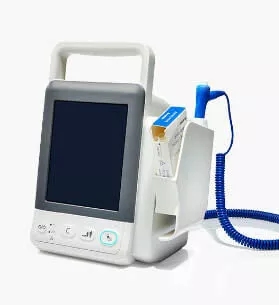
Medical Device Prototyping
At DEYUCNC®, we offer reliable rapid prototyping and rapid manufacturing solutions crafted to suit the needs of the medical device industry. Regardless of our project load, our customers can rest assured that we will deliver high quality, precision products on time and at affordable rates.
DEYUCNC Medical Device Prototyping Applications
- Handheld devices
- Medical carts
- Medical diagnosis equipment
- Medical monitor instruments
- Medical treatment devices
- Anatomical models
- Tables and panels
- Teaching aids
- Ultrasonic equipment
- Physiotherapy apparatuses
- MRI devices
- X-Ray equipment
- Clinical analytical instruments
- Care equipment
- Surgical instruments
- Electronic apparatuses
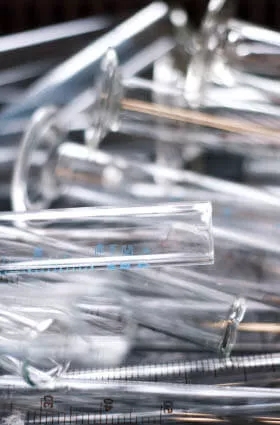
The Medical Prototyping Process
The medical device prototyping process consists of four key stages: creating alpha, beta, and pilot prototypes and crafting a final (or mature) product.
- Alpha prototypes. Alpha prototypes are usually non-functioning, reducing the cost of and time required for production. Manufacturers use these 3D printed prototypes to test product dimensions.
- Beta prototypes. Beta prototypes are generally created using more refined manufacturing techniques. These prototypes are functional but may not resemble the aesthetic design of the final product. Manufacturers use them to test for functional design or manufacturability flaws and seek out investor funding and consumer feedback.
- Pilot prototypes. Pilot prototypes are similar to beta prototypes but more closely resemble the final product. Manufacturers construct these prototypes to exact design and material specifications and use them from soft launches or clinical trials.
- Final product. The final matured product employs the finalized design that incorporates any of the desired modifications made to the previous prototypes.
How to Build a Medical Device Prototype
At DEYUCNC®, we rely on several precision machining techniques to build our clients’ medical prototypes, including:
CNC machining. Our precision CNC machining capabilities, including turning, EDM, wire EDM, surface grinding, and CNC milling services allow us to create complex 3D shapes, geometries, features, and surfaces on metal (including aluminum) and plastic substrates. The machining process produces tight tolerance medical device prototypes and products accurately and repeatedly.
Clear acrylic machining and polishing. Surface finishing operations, such as clear acrylic machining and polishing, alter the surface of the prototype or product to provide a distinct or desired aesthetic or function. These techniques can change the appearance and add other characteristics to the part, such as greater corrosion resistance or conductivity. For acrylic specifically, the machining and polishing operations facilitate the production of products with high clarity and precision, such as lenses and prisms.
Aluminum machining. Aluminum is a low-density, high-strength substance. Machining and polishing the material allows manufacturers to produce high quality, close tolerances, products, and prototypes.
Vacuum casting. Vacuum casting is ideal for creating rigid and flexible parts and prototypes. At DEYUCNC, we offer hundreds of casting polymers and a variety of color options to select from, as well as turnaround times of 15 days or less for up to 20 parts (depending on part design and volume). Compared to other prototyping methods, such as injection molding, this process provides better surface finishes and is more affordable as the molds are less expensive and more durable.
Reaction injection molding (RIM). Reaction injection molding produces strong, lightweight parts and prototypes. Compared to other injection molding methods, the process allows for more complex and intricate part geometries at a low cost per part. Additionally, in general, DEYUCNC’s injection molding services enable repeatable, high volume production (into the millions).
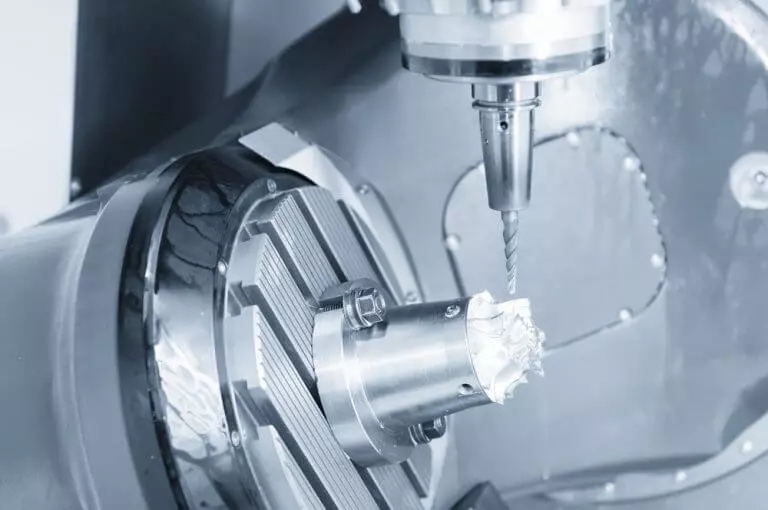
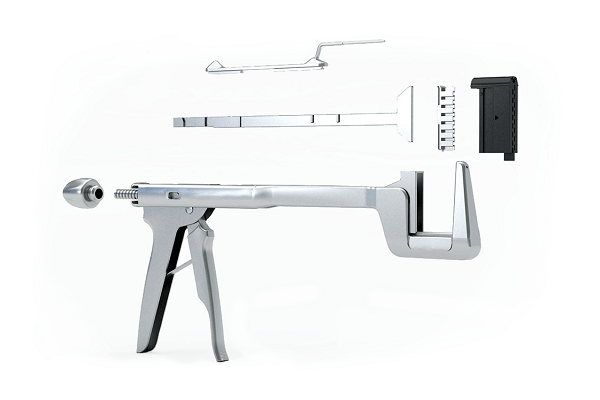
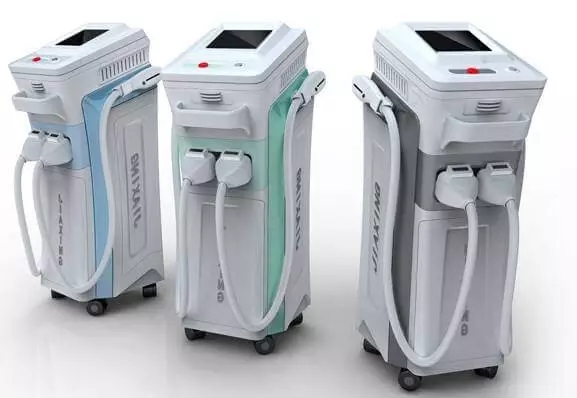